Specialist Measurements For Turbine Supervisory
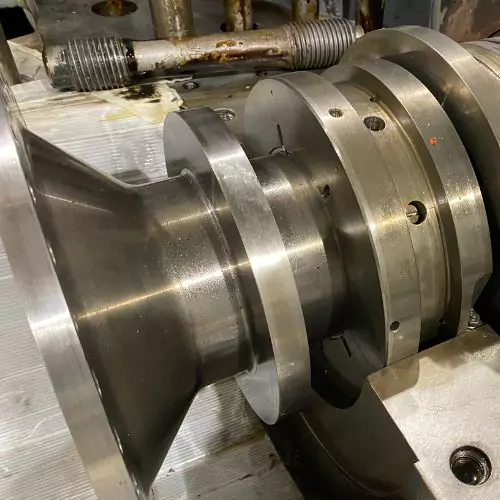
capabilities
Specialist Measurements For Turbine Supervisory
Sensonics can provide new equipment or the full retrofit project service for turbine supervisory system upgrades complimented by a range of innovative products. Our design office has many years of experience in providing instrumentation systems to match the turbine requirements in terms of mechanical integration, sensor type and signal processing.
Our experience ranges from large steam turbines (>600MW) to turbine-driven feed pumps, providing the complete suite of turbine supervisory measurements which include shaft eccentricity, differential expansion, case expansion, valve position, absolute shaft vibration, shaft position, thrust wear, reverse rotation and speed.
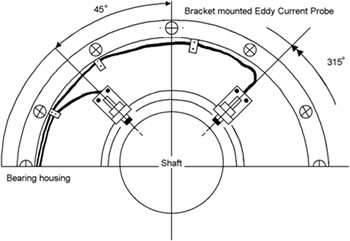
Shaft Eccentricity
Sensonics have developed a dual path eccentricity algorithm to specifically eliminate the effects runout caused by marks and dents on the shaft. The module utilises the turbine speed to actively adapt a low pass elliptical filter response to remove the high frequency components of the eccentricity waveform derived from a proximity probe. This provides accurate peak measurements of shaft eccentricity particularly at low barring speeds and is effective through the full speed range.
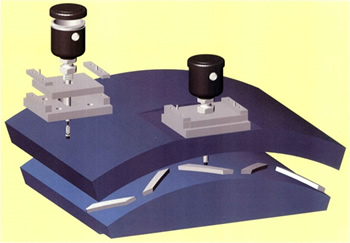
Differential Expansion Techniques
Whilst we offer large range probes and complimentary / ramp configurations for differential expansion the calibration can be complex and limited due to mechanical restrictions and temperature drift.
Our Mark Space technique operates on detecting movement in special plates attached to the turbine shaft. The shaft target pattern consists of a number of pairs of ‘teeth’ and ‘slots’ surrounding the shaft. When the shaft rotates, the voltage pulses produced by the proximity probe have a tooth to slot pulse width ratio dependent upon the axial relationship between the shaft pattern and the probe position.
Removing the absolute gap measurement and replacing it with a timing technique provides a repeatable and stable measurement over the full turbine speed range.
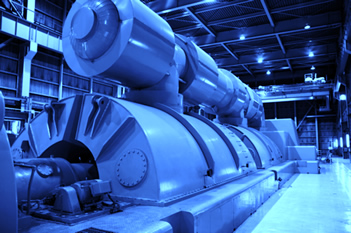
Casing Expansion
Measuring the rotor casing or shell expansion is critical to ensure the thermal characteristics of the turbine are performing as expected. As well as general expansion, this measurement, carried out with LVDT sensors, can be used to detect crabbing of the cylinder as a result of a seizure in a slider plate.
Due to the different thermal growth characteristics on start-up of the rotor and the case this measurement can also be used to determine the rotor to case differential expansion.
Robust LVDT designs and smart measurement algorithms are a key offering from Sensonics as a part of our turbine supervisory suite.
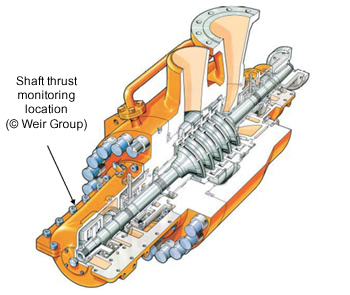
Shaft Position & Thrust Wear
The position of the machine shaft or wear of the thrust bearing pads is critical measurement on rotating machines where rotors are employed in steam, gas or fluid handling.
The challenge is to provide a repeatable measurement utilising a proximity probe in a restricted space with an accuracy of better than 10um.
Sensonics strength is in designing and supplying the right probe with enough measurement range to allow for shaft float and to avoid unwanted side target interference. Along with sensor mounting arrangements that provide mechanical adjustment in conjunction with signal processing and calibration facilities we can offer the complete package.
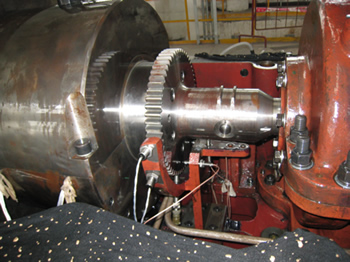
Overspeed Protection
Overspeed protection is a key requirement for the critical rotating plants where the failure of the speed governing system can lead to damaging consequences.
Independent electronic speed monitoring and shutdown is essential to reduce this risk to an acceptable level and is a standard upgrade for mechanical systems that require a physical Overspeed test to demonstrate compliance. Sensonics have been providing high integrity Overspeed protection systems for many years with proven field reliability. The architecture of our system and facilities offered has been developed in conjunction with our customers, offering up to SIL-3 integrity in combination with a range of innovative proof test facilities.
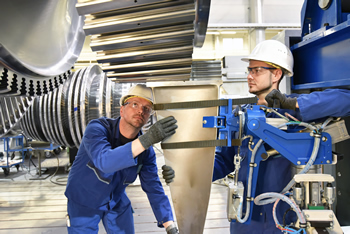
Reverse Rotation
A reverse rotation incident with large machines such as turbines and pumps can be damaging to the driven plant (such as compressors or generators) and connecting systems.
The challenge with this measurement is to provide rapid detection of the turbine movement into this state (less than 2 revolutions) and generate the appropriate alarm.
Sensonics utilise a dual probe arrangement around a single or multi-tooth wheel and can advise on the precise sensor mounting and calibration to ensure correct detection with the signal processing equipment.


Our Products
Download the engineers’ guide to specifying vibration monitoring systems
If you are designing a system which uses vibration monitoring then this guide can help you specify vibration monitoring systems.
This guide covers:
- Types of vibration sensors
- Monitoring equipment
- Questions to ask when designing or specifying a vibration monitoring system
- Why work with Sensonics
Please enter your details in the form to get your copy.
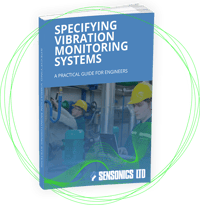
Get your copy


Have questions?
Talk to an expert
Our experienced Application Engineers are available to assist you in solving any problems that you may have concerning the choice and application of any of the Sensonics products in the measurement and control of vibration, position, temperature and proximity.
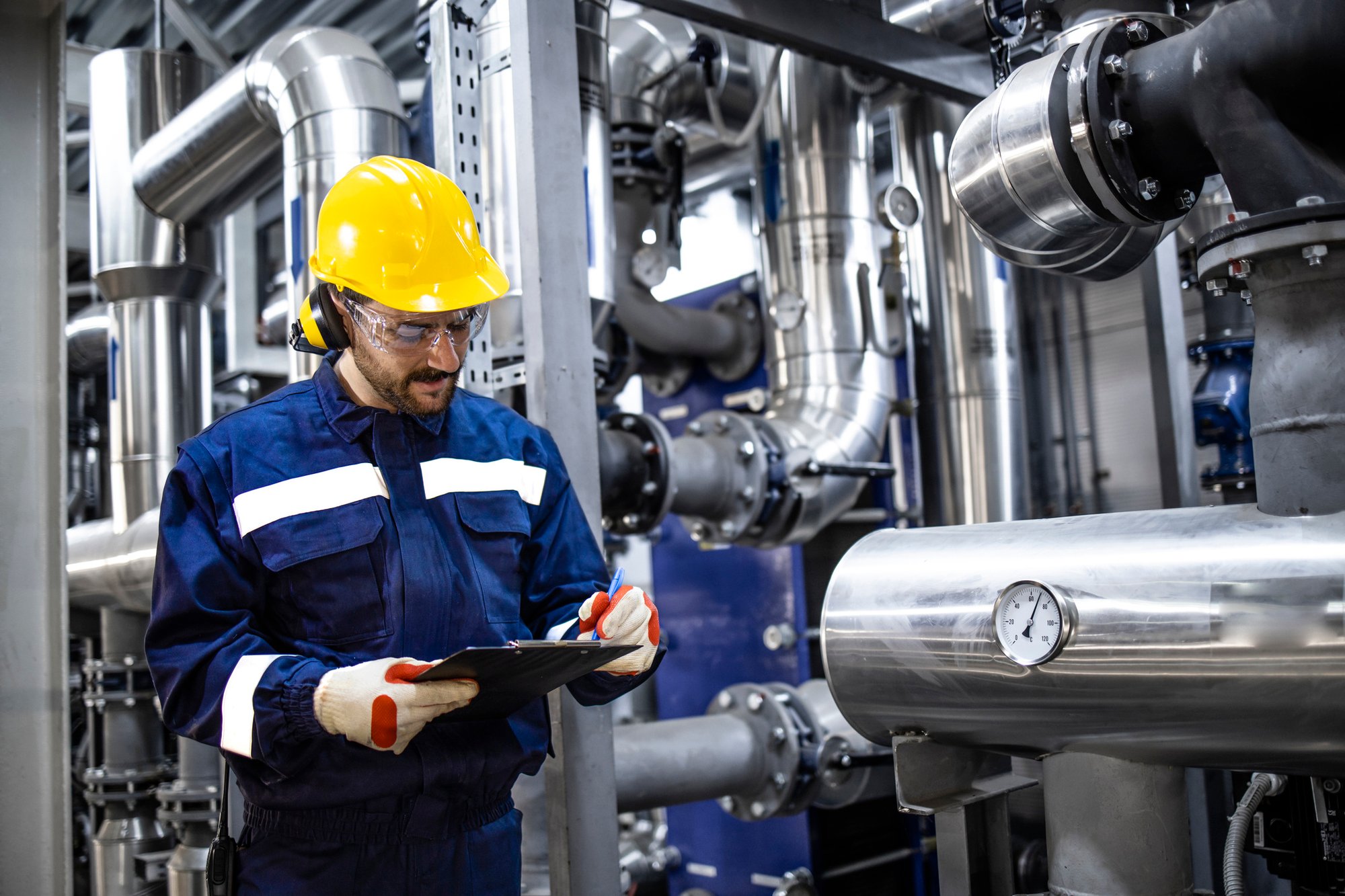